Kent Wien
Well-Known Member
I wanted to share a modification that works beyond my expectations. Ever since I put the belly pod on my Husky, I’ve had a difficult time climbing to 900 feet before the CHT on #3 cylinder would exceed 400 degrees.
So after learning that Aviat has recently redesigned the baffling behind the number 3 cylinder to accelerate the flow over that cylinder, I decided to try it. The easiest way would be to buy the right rear baffle and bypass channel as a complete set that’s riveted together. It is listed as Aviat part: Right Rear Baffle P/N 35380-504.
After this change, upon reaching 1000’ my #3 cylinder is now at 370 instead of 400-410. In cruise the #3 cylinder is the second coolest. This is on an airplane using a Powerflow Exhaust, Auto Fuel STC and a cargo pod.
Just wanted to pass this along. I believe this baffle works on all Huskies.
Kent
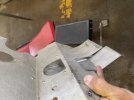
So after learning that Aviat has recently redesigned the baffling behind the number 3 cylinder to accelerate the flow over that cylinder, I decided to try it. The easiest way would be to buy the right rear baffle and bypass channel as a complete set that’s riveted together. It is listed as Aviat part: Right Rear Baffle P/N 35380-504.
After this change, upon reaching 1000’ my #3 cylinder is now at 370 instead of 400-410. In cruise the #3 cylinder is the second coolest. This is on an airplane using a Powerflow Exhaust, Auto Fuel STC and a cargo pod.
Just wanted to pass this along. I believe this baffle works on all Huskies.
Kent

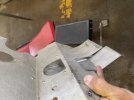
Last edited: